Laser tracker system
Dimensional checks for both individual components and assembled parts of medium and large dimension directly at the customers’ utilizing LASER TRACKER.
Thanks to this sophisticated and precise portable instrument for centesimal measurements, it can detect real dimension of an object, and the data collected are uploaded to a dedicated software to be compared with 3D Mathematics and finally the certificated pdf report is processed.
“The dimensional certainty of what has been built is a fundamental part of the project …”
-measurements of single parts of medium-large dimensions
-comparisons with 3D mathematical model
-special measurements during assembly phase
-Positioning and alignment of machinery according to selected layout
-New construction machinery surveys with reference CP assembly for the subsequent installation phase
-Obsolete machinery surveys before revamping
Many companies need to accurately measure the three-dimensional characteristics of large objects.
An increasingly widespread method is based on the use of the Laser Tracker, an instrument whose introduction dates back to the late 1980s.
As the name suggests, the Laser Tracker measures 3D coordinates by tracing a laser beam on a retroreflective lens held in contact with the object of interest.
The Laser Tracker can measure objects both up close and at a distance of 80 meters. Single point accuracy is usually about 0.002 ″.
The Laser Tracker collects coordinate data at high speed and requires only one operator for simple measurements. It improves three-dimensional measurement methods and makes completely new production methods possible.
The big car manufacturers certainly have something to say in terms of globalization:
they do not only require the supply of “just in time” components, but also require that the parts supplied are impeccables.
Quality control no longer applies only to finished products. Today, measurement technologies actively control the entire production process. If the quality of the product does not conform to the standards, companies suffer losses in economic terms and credibility with customers.
The importance of precision measurement is now a recognized reality in today’s world of production. Technological progress has also led to progress, both in terms of functions and precision, of the tools available to manufacturers today.
The range of optical and tactile measurement technologies available is wide.
The most common and basic of the tactile or contact technologies is a group of devices generally known as hand tools.
This family includes classic equipment such as micrometers and gauges which, although they are among the most used manual measuring instruments, are nevertheless not free of errors.
In this type of instrument, the accuracy of the measurement and interpretation of the results largely depends on the user.
The measurements can therefore vary greatly depending on the operator.
Furthermore, manual tools are not always able to provide all the measurement documentation that customers rightly require today.
In recent years, optical or non-contact measurement technology has been significantly improved.
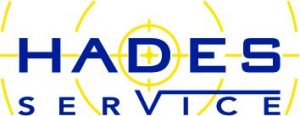
di Colombo Luca & C.
Contatti
- C.fisc./P.IVA: 02148920131
- Cell/Fax: 039.956326
- Mail: info@hades-sas.it